■ 未利用エネルギーを用いた空調・冷凍技術の研究
辻森 淳 研究室
身近にあるエアコンや冷蔵庫は、みなさんの生活を豊かにし、また、快適にするために不可欠な家電品です。しかし、これらの製品は、電力を多く消費する機械でもあります。温室効果ガスであるCO2の排出を削減し、また、夏場の日中のような電力を大量に消費する電力ピークをカットするためにも、電力駆動以外の方法で空調や冷蔵・冷凍をする技術の開発が急務になっています。また、自動車のように投入エネルギーの30%程度しか動力に変換できない状態で、さらに、そのエンジン動力から駆動力を得ているカーエアコンにおいては、燃費向上のためにも代替の空調方法の検討が必要です。
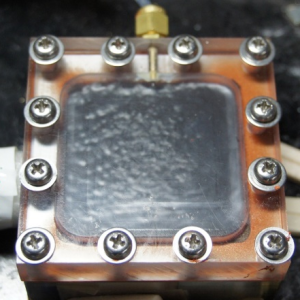 図1 等圧動作吸収器・再生器 |
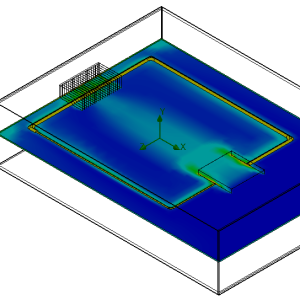 図2 3次元熱伝導解析 |
電気も熱も同じエネルギーであり、特に空調・冷凍機器においては、理論的には熱駆動が可能です。熱を駆動源とする場合、新たに燃料の燃焼熱を使用しなくても、低温廃熱や太陽熱などの未利用エネルギーの有効活用ができ、環境負荷低減だけでなく省エネルギーにも大きく貢献できると考えられます。当熱工学研究室では、熱駆動冷熱機器の一種である吸収冷凍サイクルに着目し、次世代吸収作動媒体を用いて、欠点である設置容積の大きさ、起動の遅さを改善する研究をおこなっています。さらに、人工衛星など宇宙用の冷却デバイスを応用展開し、毛管力を用いた新たな吸収冷凍サイクルを提案するとともに、実現に向けて、毛管力による圧力差保持や冷凍効果の実証などの研究もおこなっています。
■ ナノ・マイクロ空間における材料・加工プロセスの研究
柳生 裕聖 研究室
高機能でコンパクトな化学分析装置や医療用デバイスを実現可能な技術であるMEMS(微小電気機械システム)では高分子材料やシリコン基板に対し微細な加工が施されます。MEMSの加工プロセスではナノ・マイクロ空間の材料特性が重要になるため,コンピュータを用いた材料・加工プロセスの分子レベルのシミュレーションやナノサイズの材料を利用した新しい材料・加工プロセスの研究を行っています。
コンピュータを用いた材料・加工シミュレーションでは,計算規模に応じて学外のスーパーコンピュータを利用しながら高分子レジスト材料,ゴム材料の物性予測やレーザ加工,砥粒加工などの材料・加工プロセスのシミュレーションを実施しています。さらに,シミュレーションの結果から得られた情報や材料の熱,光学物性を利用した新しいナノ材料の生成・加工プロセスやマイクロ流体デバイスの開発にも取り組んでいます。特にMEMSにおけるレジスト材料などの高分子材料のメソ領域の材料特性に注目し,その特性のマイクロシステムへの応用を目指しています。
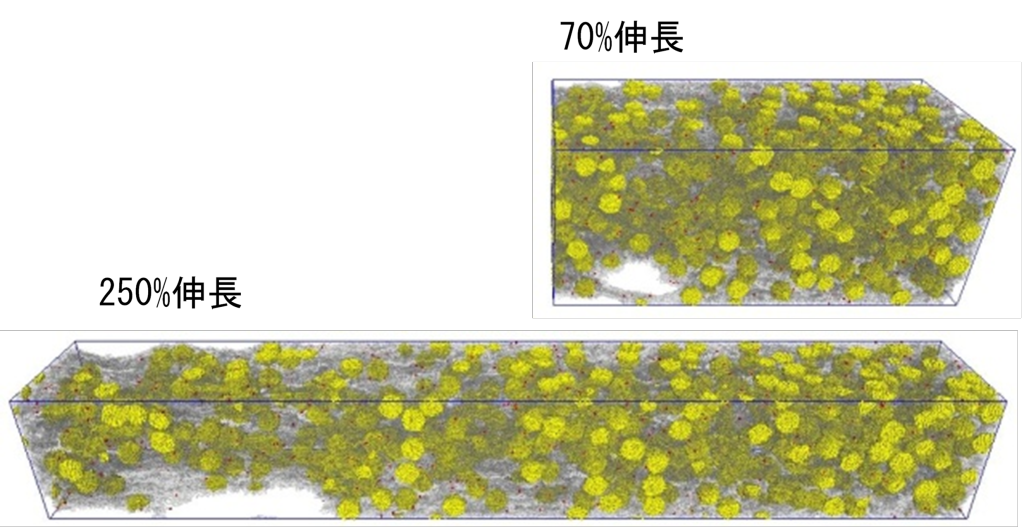
図1 フィラー充てん高分子材料の伸張シミュレーション結果
粗視化分子動力学法により並列計算機を用いてナノフィラー(黄色の粒子)が充填された高分子材料の伸張挙動を解析することで,ナノフィラーの分散状態などの材料の微細構造と力学物性の関係を明らかにすることが可能です。
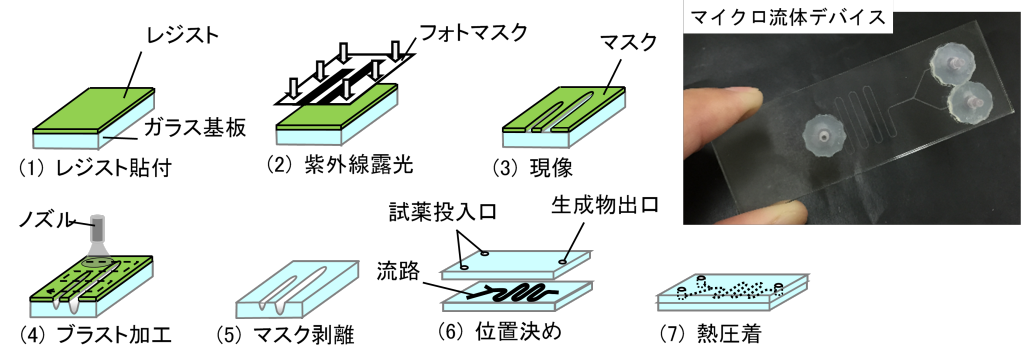
図2 マイクロ流体デバイスの製造プロセス
微細加工プロセスにより微細流路(幅200 μm,深さ100 μm)を有するガラス製マイクロ流体デバイスを作製しています。研究室ではこのデバイスを利用して液相還元法による金属ナノ粒子の合成を検討しています。
■ 「曲がり穴」を自由に開けるには…
内山 光夫 研究室
自動車部品の中には、アルミニウムやプラスチックなどから作られているものが数多くあります。それらの部品は、金型という金属製の型を用いて製造されますが、金型の温度管理を精密に行なわないと製品の品質や精度を保つことができません。そのため金型の内部には、冷却液を通す通路が複雑に設けられています。しかし、現在の技術ではまっすぐな通路しか加工できないため、金型の温度管理を十分に行なえません。そこで、求められているのが「曲がり穴」なのです。
曲がり穴については従来からさまざまな研究が行われていますが、本研究では非常に簡単な構造で曲がり穴を開ける技術について開発を進めています。具体的には、図1のように柔軟性のある工具が曲がりたい方向に少し加工した後に、工具を押し入れていくと工具は加工された側に曲げられていきます。この動作を繰り返すことにより曲がり穴を加工するという考え方です。
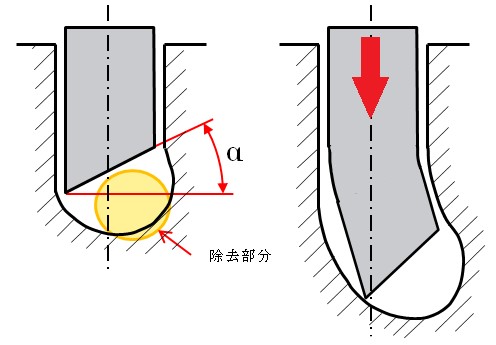
図1 曲がり穴の加工原理
研究では実際の加工を行う前に、図2のように数値解析を行い最適な工具形状と加工条件を求めます。その結果加工できた曲がり穴が、図3に示した写真です。
|
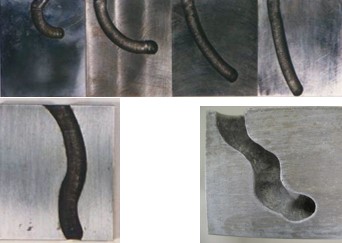 |
図2 数値解析の結果 |
図3 曲がり穴の加工事例
|
現在は、この曲がり穴の加工速度を向上させるため、公的研究資金(NEDO)の支援を受けて研究を進めています。
■ さまざまなコミュニケーションロボットの協力による対人サービス作業の向上化の研究
小松 督 研究室
ロボットにはさまざまな作業が期待されていますが、人と同じように多くの作業を1台でこなすことのできる汎用ロボットは実現が難しく、また実現しても高価なものになって、広く導入されにくいと考えられます。そこで、1つの機能に特化した、安価な専用ロボットを、作業を限定して導入したり、あるいは複数台使って協調システムを構築して、多くの作業に対処したりすることが、主に力作業の分野で広くおこなわれています。
一方、今後広く利用が期待されるコミュニケーション機能を持ったサービスロボットが対象とする対人サービス作業においても、状況は同じです。そこで、本研究では、力作業での協調作業の考え方を対人情報サービス作業にも適用することをおこなっています。ここで取り上げる作業の内容は、会話をする、情報を提供する、パフォーマンスをするなど、サービスの中でも力作業以外のものです。そして、1台のロボットがすべておこなうのではなく、それぞれの作業が得意な、いわば専用のサービスロボットを複数台用意し、わたしたちがグループ作業でよく使っている「役割分担」という知識をロボットに応用することで、提供できるサービスの幅を広げ、効果を向上させることを目標としています。
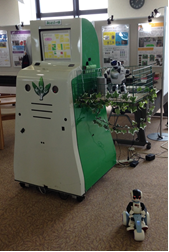
図1 3台のロボットによる協力システム(左からKei-4、 パルロ、 ロビクル)
■ 日本発・ディジタルものづくり規格(DTPD)による設計の効率化検証
金田 徹 研究室
DTPD(Digital Technical Product Documentation)という新しい日本工業規格ができつつあります。これは、3D-CADによる製品のディジタルデータを、設計・開発・製造のプロセスではもちろんのこと、製品企画から顧客へのアフターサービスの全プロセスで活用させようという趣旨のもとで規格化が進められていいます。本研究では、この規格原案作成に協力しているJEITA(電子情報技術産業協会)が主催し、(公社)日本設計工学会が後援する実証プロジェクトに参加し、3Dモデルを活用したものづくりの効率化の検証をおこなうことにしました。
JEITAから与えられた課題は、小型プリンタの樹脂製外装部の設計モデルを、GPS(製品の幾何特性仕様)の考え方を取り入れて構築することでした。3D-CADであるSolidWorksを使用して、2つの設計案を検討しました。その後、問題点の解消をした上で、この樹脂製品を製作するための金型要件も満足させた最終設計案を決定しました。その外観を図1に示します。
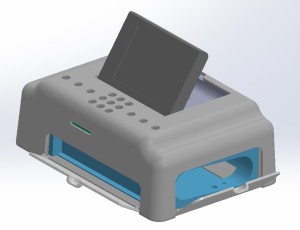
図1 最終設計案(外観のイメージ)
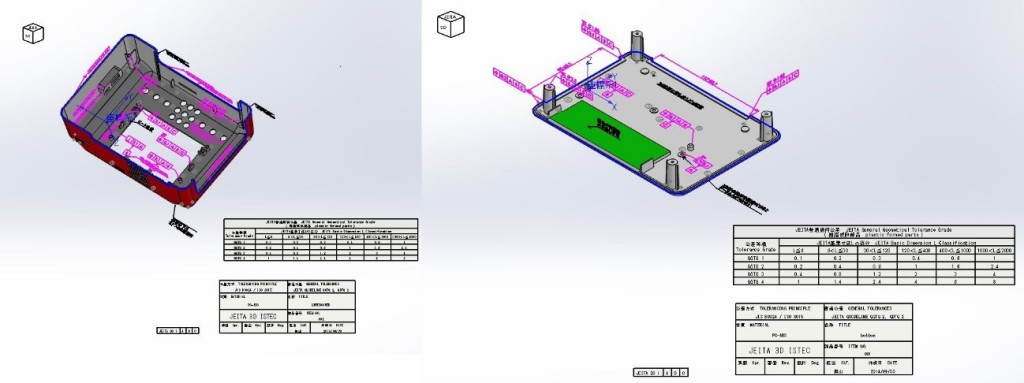
図2 図示された3DAモデル(左と右:外装部の上部品と下部品)
最終設計案として作成した3Dモデルを3DAモデル(寸法以外に製品・部品に必要な情報を含んだモデル)に仕上げられた状態の一例を図2に示します。
3DAモデルによるものづくりの効率と従来通りの2D図面によるものづくりの効率を比較する必要があります。2D図面には、数多くの寸法の指示や寸法公差、幾何公差、表面性状などを付け加えなければなりません。しかし、3DAモデルにも、そもそも寸法情報は、ディジタルモデル自身に含まれていることが、図示状での大きな違いとなります。
その結果、DTPD規格を適用した3DAモデルによる設計と2D図面による設計では、その工数はほぼ1/2以下になることが実証できました。
この実証プロジェクトには、8大学、2高専の合計10チームが参加しましたが、本学チームは準優勝の結果を残すことができました。